7 Stunning Use Cases For 3D Printing In Medical Field
- Woo Mo Sik
- Feb 14, 2022
- 7 min read
Updated: May 14, 2023
3D printing, or additive manufacturing, is revolutionizing the medical industry over the past decade. Medical professionals are utilizing 3D printing technology to develop new medical tools, orthopedic implants, and prosthetics as well as the customized replicas of tissues, bones and organs.

3D printed hip implant with new generation of biomaterial that has excellent biocompatibility and promotes bone healing.
Table of Contents
Rising of 3D Printing in Medical Field
According to the Global Market Insights, healthcare 3D printing market size was valued at over USD 1.7 billion in 2020 and is estimated to expand with a CAGR of more than 22.3% between 2021 and 2027.

North America dominates the market for healthcare 3D printing possessing 40% of the market’s shares, valued for over USD 701.4 million. Credit: Global Market Insights
The increasing support for quality control and safety measures from FDA is largely driving the industry development in North America. Additionally, a higher intensity of research and development activities is noted in North America by academic institutions as well as manufacturers.
Benefits of 3D Printing for Patients and Doctors
Personalized Healthcare

Shapeshift production process for customized wearables. Credit: 3D Natives
With recent technology and material advance, additive manufacturing allows for the design and print of more complex designs and material options than conventional manufacturing method. Healthcare professionals can now easily create customized medical tools and implants that are perfectly adapted to a patient’s anatomy, or a specific surgery.
The better fit of prosthetics and implants can drastically reduce the chance of infection, provide pain-free functions and speed up the recovery process.
Fast Design and Production
Traditional prosthetics and implants can take weeks to design and manufacture, especially if they are custom made for a patient.
With 3D printing techniques, healthcare professionals can design and print the object in-house on a professional 3D printer within a few days (and sometimes even less), which is much faster than molded or machine parts.
This could significantly reduce patients’ waiting time and lower the chances of complications that may occur as a result of delayed or unavailable medical devices.
Increase Cost Efficient
3D printing provides patients with affordable tailor-made prostheses and implants that are so expensive in traditional manufacturing processes. There is also no need to make any specialized tooling, jigs or fixtures, and there are no minimum volume requirements.
The entire process – from scanning, to 3D modeling and printing – can be performed simply by a single person and an inexpensive desktop 3D printer, saving time, labor, and money.
Real-life Applications of 3D printing in medical field
1. 3D Anatomical Models for Surgical Planning

Tumor removal surgery performed with 3D planning at SJD Barcelona Children's Hospital. Credit: SJD Barcelona Children's Hospital
In 2013, SJD Barcelona Children's Hospital used 3D printing to plan the first-ever complex cancer surgery in a 5-year-old boy with great success. The boy was diagnosed with neuroblastoma, a rare childhood cancer develops in nerve tissues. To remove the tumor without endangering the patient’s life, surgeons had to skillfully avoid cutting the blood vessels and surrounding organs.
After two unsuccessful attempts, the team created a life-sized, 3D printed replica of the boy's tumor using materials with texture similar to the organs. Using the 3D model, surgeons carefully analyzed the anatomical relationships of tumor, vessels and organs and simulated the highly complex tumor excision. After rehearsing for more than a week, the surgeons successfully removed the tumor from the boy’s body. And the boy was expected to fully recover without additional surgeries.
Since then, 3D technology has been implemented by the hospital professionals in around 100 surgeries since 2017 to plan complex surgical procedures, create cutting guides and surgical tools, design patient specific prostheses and implants. Currently, 3D printing has been rolled out to other specialists in the Hospital including traumatology, maxillofacial surgery, cancer surgery, neurosurgery, cardiology, plastic surgery and dental surgery.
2. Prosthetic limb

Prosthetic socket is tailored to fit the leg of each patient using 3D technology. Credit: University of Toronto Scientific Instruments Collection
There are more than 57.7 million people living with limb loss worldwide. While prosthetic devices can help patients getting around more easily, they remain too expensive and uncomfortable. The problem has become even more obvious in children with limb loss – they outgrow prosthetics quickly and require frequent replacement. It costs an average of USD 80,000 per limb to keep a child outfitted with an appropriate prosthetic.
Using 3D printing technology, the University of Toronto introduced a low-cost, time-saving way to produce custom fit leg socket for children. The process is simple: a technician scan the residual limb, model a socket based on the 3D scanned data, and press "print". After 6 to 9 hours, a socket that is designed specifically for the patient will be ready.
3. Mass Production of Emergency Medical Supplies

3D printed finger splint designed by Ian McHale for temporary stabilization of a finger or joint after an injury. Credit: Thingiverse
Ian McHale, a senior at Steinert High School in United States, developed a design for producing finger splint on a low-end 3D printer in about 10 minutes for less than USD 2 cents of recycled plastic.
McHale understood the difficulties for developing countries in ordering large supplies from overseas, let alone custom splints. That’s why McHale decided to design 3D printed finger splints that were more affordable and readily available. Depending on the platform size, 30 – 40 splints could be printed in a single run. This splint design is also beneficial to clinics, remote hospitals and first-aid posts when supplies run low or special medical tools are required.
McHale’s design won the first prize in his division at the Mercer Science and Engineering Fair and was awarded by the United States Army and Air Force. He believed with a 3D printer, splints can be created on an individual basis and modified to fit various finger sizes. Currently, his design of the 3D printed finger splints is available for free downloading at Thingiverse and he invites people to design their personalized finger splints.
4. Bone Replacement

The KMU Hospital 3D printed an artificial collarbone (clavicle) using PEEK instead of traditional titanium alloy for bone replacement. Source: 3Dnatives
In 2018, the medical team at Kunming Medical University Hospital (KMU Hospital) in China, in collaboration with the 3D printer company IEMAI 3D, successfully transplanted the world's first 3D printed PEEK collarbone. This was performed on a 57-year-old man with advance cancer whose collarbone had to be cut off to remove cancer cells from affected tissues and organs.
To fix the collarbone after resection, doctors at KMU Hospital decided to use a PEEK prosthesis instead of using the traditional titanium mesh – as it won’t affect the patient's later treatment with chemotherapy. PEEK also guarantees faster recovery and demonstrates no side effects to patients.
The introduction of PEEK, ULTEM, PMMA and other thermoplastics to the medical field is opening the way for more patients to undergo implant surgery, as it would not affect their possible future treatments.
5. Skull Reconstruction

Tiffany Cullern underwent surgery to remove a brain tumor and had her skull constructed with a 3D printed skull implant after complications. Source: All3DP
Tiffany Cullern, a 20-year-old girl in Britain, had her skull reconstructed with a 3D printed skull plate.
The young girl suffered from a extremely rare brain tumor. The tumor was a size of a golf ball and kept growing. While surgeons were able to removed the tumor, Cullern was unresponsive with her brain swelled after the surgery. Surgeons could only undergo another operation to remove her skull in order to relive pressure. Since doctors were unsure whether Cullern’s brain would swell again, they leave her skull out until the condition was stable.
Leaving the head with a hand-sized hole for 3 months, Cullern was finally implanted with a 3D printed skull piece made of titanium, plastic, and calcium. She recently got engaged to her boyfriend and is thankful to have her head back to normal and is happy to move on in her life.
6. Human Corneas
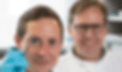
Dr Steve Swioklo and Prof Che Connon successfully 3D printed the world’s first human cornea. Credit: Newcastle University
In 2018, the first human corneas was 3D printed by scientists at Newcastle University in United Kingdom.
The researchers worked by mixing healthy corneal stems cells with alginate and collagen to create a printable solution – “bio-ink”. Using a simple 3D bio-printer, the bio-ink was successfully extruded to form the shape of a human cornea in less than 10 minutes.
3D printed corneas were designed according to patient’s unique specifications. By scanning a patient’s eye, researchers could use the data to rapidly print a cornea which matched the size and shape.
Although the 3D printed corneas still require further testing before they are usable for transplant, the scientists at Newcastle University believed 3D printed corneas could relieve the global shortage of donor corneas in near future.
7. Heart Valves

A 3D printed artificial heart valve. Source: 3D Printing Indutry
Jonathan Butcher and his team at Cornell University pioneered 3D tissue printing technology to create living heart valves that possess the same anatomical structure as native valve.
To precisely produce an artificial valve, Butcher’s team had developed algorithms that process 3D image datasets of a native valve and automatically form the full 3D model of the heart valve. Bio-printing is then conducted in a dual syringe system with a mixture of alginate/gelatin hydrogel, smooth muscle cells and valve interstitial cells to mimic the structure of the valve root and leaflets.
Butcher believed bioprinting would gain much more traction in the tissue engineering and biomedical community over the coming years. The patient-specific tissue models would help healthcare professionals in learning disease pathogenesis and screening drug efficacy, or making living tissue replacements tailored directly to patient geometry.
Time to Get Started with Medical 3D Printing!
It is obvious that the trend of using 3D printing in medical field will keep growing, and it is time for us to utilize it to improve patient care.
If you find too complicated to start everything on your own, you can consider consulting with experienced companies. Novus provides medical grade 3D printing filament and 3D printing services for hospitals, researchers and vets.
Contact our expert advisors today at info@novusls.com for a free consultation.